Moderne Leichtbaumaterialien lassen sich meist nur schwer mit herkömmlichen Verfahren prüfen. Bei diesen Materialien kann die luftgekoppelte Ultraschallprüfung ihre Stärken ausspielen. Für viele Anwendungsfälle ist die Luftultraschallprüfung eine Option. Insbesondere bei Leichtbaumaterialien kann sie ihre Stärken voll ausspielen.
Leichtbaumaterialien
Auf Masse zu verzichten spart Energie. Typische Einsatzfelder dieser modernen Materialien sind Automobil, Schienenfahrzeuge, Luft- und Raumfahrt, aber auch die Bauwirtschaft.
Um die mechanischen Eigenschaften von Stahl, Aluminium, Beton und anderen konventionellen Materialien zu erreichen oder zu übertreffen, werden häufig Verbundmaterialien verwendet. Dazu gehören mit Glas- oder Carbonfasern verstärkte Kunststoffe, Sandwichstrukturen mit Schaum- oder Wabenkernen oder auch Textilbeton. Auch die Fügetechniken haben sich mit diesen modernen, kunststoffbasierten Materialien verändert. Wurde früher eine Metallkonstruktion geschweißt, genietet oder verschraubt, so wird heute sehr oft geklebt. Sowohl für die Verbundmaterialien, aber auch für die Klebeverbindungen müssen neue Prüfverfahren entwickelt und getestet werden.
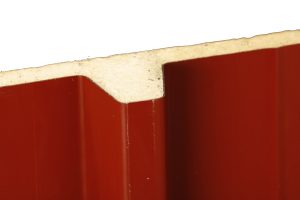
Typische Ungänzen
Die große Stärke der Luftultraschallprüfung besteht im Auffinden von unerwünschten inneren Grenzflächen. Das können Delaminationen, Lufteinschlüsse oder fehlender Klebstoff sein.
Eine oft gestellte Frage bei geklebten Materialien ist die Qualität des Klebstoffauftrages. Überall dort, wo der Klebstoff in der Fügeverbindung fehlt, ist eine schlechte Haftung und damit eine mangelnde Qualität des Gesamtbauteils vorprogrammiert. Fehlender Klebstoff führt zu Hohlräumen oder Delaminationen (teilweise innere Ablösungen). Bereits kleine Bereiche von wenigen Quadratmillimetern Fläche können mit Luftultraschall sicher detektiert werden. Andere schlecht haftende Verbindungen, die zum Beispiel durch eine schlechte Oberflächenvorbehandlung oder falsche Prozessparameter entstehen, können prinzipiell auch detektiert werden. Es ist meist eine qualitative Aussage im Vergleich zu einer ordentlichen Klebung möglich. Die Bestimmung von quantitativen Parametern wie z. B. eine Haftfestigkeit ist derzeit noch Gegenstand der Forschung. Delaminationen entstehen in faserverstärkten Kunststoffen auch durch mechanische Schädigungen. Kunststoff bekommt keine Beulen, sondern es bilden sich entweder kleine Risse oder es kommt bei weiterer Belastung zu einer Ablösung von Schichten im Inneren des Bauteils. Diese sind ebenfalls sehr gut mit luftgekoppeltem Ultraschall detektierbar. Generell bestehen bei allen Fehlern, die mit einer Veränderung der (lokalen) mechanischen Eigenschaften des Materials verbunden sind, gute Chancen sie mit Ultraschall detektieren zu können. Beispiele sind die Dichteänderung in Keramik oder Beton durch Agglomerationen oder Fremdkörper und Feuchtigkeitsschwankungen in Holz. Risse können dann detektiert werden, wenn sie sich quer zur Schallrichtung ausbreiten. Eine Ausnahme sind Risse, die durch das Bauteil komplett hindurch gehen. Ähnlich wie bei der Lecksuche können auch bei der Materialprüfung feinste Risse mit Ultraschallwellen aufgespürt werden. Kleine Fehler wie Poren können dann gut detektiert werden, wenn sie nicht einzeln sondern in größerer Anzahl auftreten. Dann ist es auch möglich Poren im Bereich von einem Millimeter aufzuspüren. Solche ein Porennest ist im Prüfbild als Ganzes erkennbar, auch wenn die einzelne Pore nicht abgebildet wird.
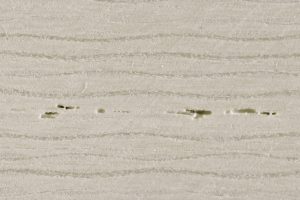
Prüfbare Geometrien
Der Stand der Technik ist das Prüfen von Platten und anderen Bauteilen, bei denen die Dicke im Prüfbereich konstant ist. Auch die Prüfung von gekrümmten Oberflächen ist möglich.
Allerdings müssen die Wandler immer senkrecht zur Oberfläche geführt werden, was in diesen Fällen erhöhte Anforderungen an den Scanner oder Prüfroboter stellt. Die mögliche Dicke der Prüfobjekte hängt in erster Linie vom Material und dem Aufbau des Bauteils ab. Eine generelle Aussage ist hier nicht möglich, jedoch liegen die Stärken der Luftultraschallprüfung im Vergleich zur konventionellen Ultraschallprüfung bei der Durchschallbarkeit sehr dicker Bauteile. Gewisse Einschränkungen gibt es bei der Prüfbarkeit von kleinen Flächen, da es durch die räumliche Schallausbreitung im Prüfkörper zu Interferenzerscheinungen mit inneren Echos im Bereich von Ecken und Kanten kommen kann. Solche geometrischen Artefakte lassen sich aber durch eine intelligente Bildbearbeitung reduzieren. Die üblicherweise verwendete Durchschallungsprüfung setzt die beidseitige Zugänglichkeit am Prüfkörper voraus. Der Größe sind dabei nur durch den technischen Aufwand für einen Scanner Grenzen gesetzt. Bei Endlosplatten oder Bändern wird hingegen ein festinstallierter Linienscanner verwendet, unter dem das zu prüfende Material hindurchgeführt wird. Ist der Prüfling nur einseitig zugänglich, kann unter Umständen auch die sogenannte Lamb-Wellen-Technik zum Einsatz kommen.
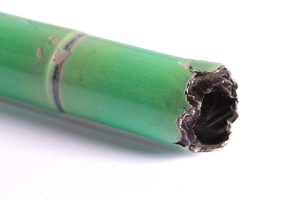
Sie müssen den Inhalt von reCAPTCHA laden, um das Formular abzuschicken. Bitte beachten Sie, dass dabei Daten mit Drittanbietern ausgetauscht werden.
Mehr Informationen